Magnesium alloy die castings
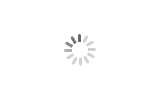
Magnesium alloy extrusion process : heating ingot → primary extrusion → cutting intermediate billet → heating → secondary extrusion → artificial aging → stretching and straightening → cutting head and tail and taking sample → roll Straightening → manual straightening → inspection → cutting and printing → oxidation coloring → finished product inspection → packaging → storage. Process characteristics: Magnesium alloys are only allowed to be heated in air resistance furnaces; in order to prevent burning, the highest heating temperature of various alloys is 470℃; the highest extrusion speed is 20m/min, which is faster than hard aluminum alloy, but only soft About 1/3 of the alloy; the shrinkage rate of the magnesium alloy extruded material is larger than that of the aluminum alloy, so the die size should be enlarged accordingly; the material should be heated to 150℃~250℃ during the tension correction, while the aluminum alloy material is at room temperature Straighten.
The production process covers investment casting, permanent mold casting, die casting, sand casting, forging, and CNC machining, stamping, progressive stamping. The materials cover stainless steel, carbon steel, brass, aluminum, zinc, gray and ductile iron, etc. For many years our products such as auto accessories, diesel engine parts, shipping accessories, agricultural machinery accessories, machinery accessories and parts have been exported to some Europe countries and USA.
We have a team of professional engineers experienced in the metal manufacturing field in China. We aim to provide our customers the quality products at competitive price with our professional service. Our engineers will evaluate and study every enquiry and design the production process best fit for the enquiry in term of cost and quality. Our inspection team will follow up the process of the production and monitor the quality of the products before shipment.